PROCESSING TECHNOLOGY
&
Facilities
At Toyota Textile, we combine various processing techniques to create yarns that meet your specific needs.



Gas Singeing
What is Gas Singeing?
Gas singeing is a process where each individual thread is passed through a gas burner flame to burn off fuzz and lint. Yarn that has undergone this process is also called "gassed yarn". We can adjust the singeing rate according to the yarn's use and count.
Benefits of Gas Singeing After gas singeing, the yarn becomes fuzz-free, noticeably more lustrous, and smoother to the touch. This process:
-
Enhances the product's value by improving its feel
-
Helps in manufacturing processes where fuzz can be problematic (e.g., smoother weaving or knitting)
-
Can be used for heat-reactive treatments in functional materials (e.g., wearable clothing, fishing line)
-
Our Unique Technology Maintaining consistent gas temperature is crucial for stable quality. Uneven singeing can lead to uneven dyeing, which isn't acceptable for high-value products. Over-singeing can burn the yarn, so high skill and experience are essential. Our skilled artisans use their expertise to bring out the best in each material.
We handle single, double, and triple yarns from 10/2 to 100/1 count. Besides cotton, we can process various materials including TC (Tetron blend), linen, wool, silk, and even polyester spun yarn in some cases.
We can adjust the singeing rate based on your specific needs and yarn count. Our facility is equipped with gas singeing machines from SSM, a European textile machinery manufacturer, as well as our original gas singeing equipment co-developed with a Japanese textile machinery maker (supported by the 2015 Manufacturing Subsidy).
Yarn Twisting
What is Yarn Twisting?
Just as the name suggests, yarn twisting is a process where we add twist to single or multiple strands of yarn.
Benefits of Yarn Twisting By twisting yarn, we can:
-
Increase its strength
-
Combine different materials
-
Improve durability compared to single-yarn fabrics
-
Maintain high quality for longer periods
Yarn twisting is also crucial for industrial yarns, enhancing their strength for various applications. We can adjust the twisting count to meet specific needs, which affects the texture and feel of knitted or woven fabrics. Typically, we follow our customers' specifications for twisting count.
Key Advantages:
-
We can create yarns with the right count and strength for specific uses
-
Twisting reduces fuzz by incorporating it into the yarn structure
-
Increased yarn strength leads to better durability and sustained high quality





ヒートセット加工前後 Before and after heat set
Heat Setting
What is Heat Setting?
Heat setting is a process where yarn is placed in a sealed chamber made of thick iron plates. Using a motor pump, we create a vacuum in the chamber by extracting the air. Then, we spray steam (produced by a boiler) into this vacuum environment.
Benefits of Heat Setting This process is essential for high-twist yarns (yarns with many twists per inch). Here's why it's so important:
-
Prevents Tangling: Highly twisted yarns tend to coil back on themselves, causing tangles (snags or kinks). These can lead to needle breakage and fabric defects during knitting.
-
Uniform Steam Penetration: The vacuum ensures even steam distribution, stabilizing the yarn's structure.
-
Increased Strength and Improved Texture: The process enhances the yarn's strength and feel.
-
Easier Weaving and Even Dyeing: Heat-set yarns are much easier to weave and dye more evenly.
Key Advantages:
-
Provides necessary moisture content for natural fibers
-
Reduces twist liveliness in high-twist yarns, making them easier to handle
-
Helps prevent skew in knitted fabrics
-
Increases yarn strength
-
Improves yarn texture, making it easier to weave and dye evenly
However, it's crucial to set the right humidity, heat retention time, and moisture content for each type of yarn. At our company, we use our extensive experience and know-how to provide optimal processing tailored to each yarn's characteristics.
Rewinding Process
What is Rewinding?
Rewinding is the process of re-spooling yarn. During this process, we can apply wax coating or perform Uster processing.
WAX Coating (Rewinding) When yarn is used for knitting, we need to apply wax to its surface to improve smoothness and knittability. This makes the knitting process much smoother.
We typically use paraffin-based wax, but we may also use silicone types or special waxes depending on the material and intended use.
Wax coating is especially crucial for yarns used in complex fabric structures. Along with wax coating, we rewind the yarn onto cone-shaped spools that allow for easy unwinding. We can also divide into smaller packages if needed.
Uster Processing Uster processing uses a capacitive method to measure variations in yarn thickness based on the material and count. It detects and cuts sections where the yarn capacity (thickness) is larger than normal.
This process helps to:
-
Remove defects that could cause needle breakage in knitting machines
-
Reduce waste by keeping defects within acceptable limits during fabric inspection
We place the Uster device (which detects slubs, neps, and other yarn impurities) just before the waxing equipment to remove defective parts of the yarn.
Important Notes:
-
According to machine manufacturers, the maximum defect removal rate is about 70%. For very fine or numerous defects, some may remain.
-
For spun yarns, which are naturally bulky, too many defects can lead to excessive cutting. This can result in a yarn full of joins, potentially compromising product quality. In some cases, Uster processing might not be feasible for such yarns.

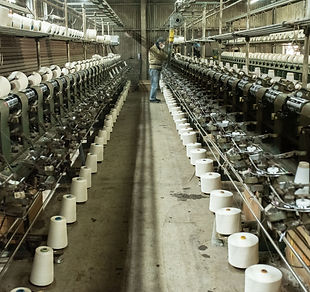.jpg)

リワインド加工 Rewind processingWinder processing

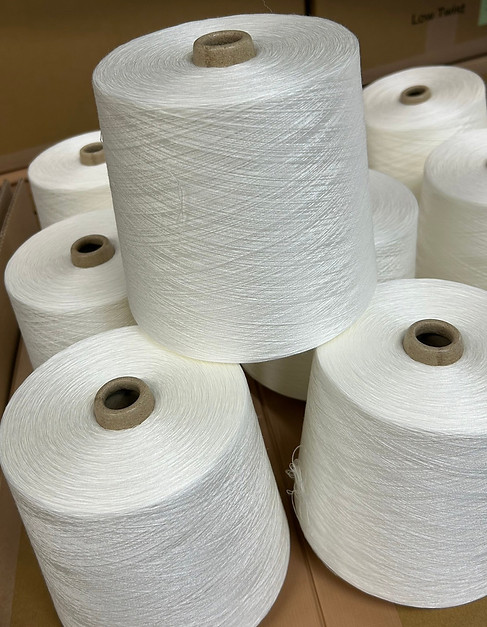
By combining these processing techniques,
we can create yarn of superior quality.
Examples of Processing Combinations:
-
Gas singeing + WAX
-
Two-ply yarn + Heat setting + WAX
-
Two-ply yarn + Heat setting + Gas singeing + WAX
-
Three-ply yarn + Heat setting + WAX
-
Three-ply yarn + Heat setting + Gas singeing + WAX
-
Single yarn with additional twist + Heat setting + WAX
-
Single yarn with additional twist + Heat setting + Gas singeing + WAX
-
Single yarn with additional twist + Heat setting + Two-ply yarn + Heat setting + WAX
-
Single yarn with additional twist + Heat setting + Three-ply yarn + Heat setting + WAX
-
Single yarn with additional twist + Heat setting + Three-ply yarn + Heat setting + Gas singeing + WAX
We can also provide custom processing combinations to meet your specific needs. Please don't hesitate to consult with us about your requirements.